Commissioning of a Robotised Palletising Line at KANN
- Quadra South Africa
- Aug 15, 2024
- 4 min read
Updated: Aug 26, 2024

Between tradition and modernity, Kann is a family business synonymous with quality and reliability since 1927. Its success is based on an irreproachable customer service policy and a constant quest for innovation, both in the development of new products and in the optimisation of existing products and processes. Kann expects the same high standards from its suppliers and partners. As a leading German manufacturer of concrete products for outdoor areas, such as paving stones, slabs, fences and steps, the Kann brand stands for top quality, sophisticated design and a natural appearance.
Recently, as part of the modernisation of its Neumarkt site, Kann chose to equip the plant with a robotised palletising system to replace the old conventional equipment. Quadra, a French manufacturer of automated equipment for the concrete industry, supplied the new facility. In addition to the benefits in terms of productivity and quality, the technical solution proposed by Quadra was perfectly in line with Kann's sustainable development strategy, which focuses on reducing its energy footprint, carbon neutrality and employee well-being.
Kann's commitment to sustainable development
At Kann, sustainability is more than just a nice word. It is a corporate culture in everyday life. As a Blue Angel (Blauer Engel), Kann is working ambitiously on its sustainable development strategy. Gradually, the company is creating new measures and implementing them consistently. CO2 neutrality was an important first step, achieved by 2022. The same goes for optimising the energy mix, with more renewable sources (solar electricity generation, heat recovery and closed water cycles) and eco-design of products, which already contain 40% recycled raw materials.
Internally, this is reflected in the careful, social and human management of our employees. The company culture is based on dialogue, respect and the sharing of common objectives between employees and management, to ensure the manufacture of quality products. In addition to training, employees benefit from an attractive and safe working environment, with machinery maintained and controlled to high safety standards deployed throughout Kann's 20 production units spread across Germany and along the border with France.
Kann and Quadra first met in 2018. Contact was easy, as Quadra's management is German speaking. ‘We organised visits to our customers in France to show them our machinery at customer’s plants,’ explains Yannick Ancrenaz, Quadra's Managing Director. Kann's technical management was quickly won over by the innovative and robust nature of the equipment supplied by the French manufacturer. They were
impressed by the level of automation in the factories they visited, and in particular by the versatility and speed of the Kuka robots installed on the sites' grinding and/or palletising lines.
Over the next 5 years, Kann consulted Quadra from time to time, an opportunity for the French manufacturer to demonstrate its ability to be present over the long term and to offer innovative solutions. Over the years, the two companies developed a solid relationship of trust, culminating in the signing of their first order in May 2023 as part of a project to replace the palletising system at Kann's Neumarkt site.
Here again, Quadra stood out among the suppliers consulted: it was the only one to offer robotised palletising, while the others stuck to the traditional gantry crane option. Quadra's offer was chosen, as it offered a better ROI in terms of reduced maintenance costs and lower energy consumption. Overall, the solution envisaged by Quadra better met Kann's concerns in terms of sustainability, as well as the safety requirements stipulated in the project specifications.
A fully automated palletising solution
The special feature of the Neumarkt plant is that it operates 3 shifts, 24 hours a day. The choice of robot was based on its lifting capacity. Given these requirements, the KR 700 model from Kuka was proposed and selected for this project. With 4-axis operation, this palletising robot has a lifting capacity of 700 kg, equivalent to a load of
350 kg of concrete products. It is equipped with a versatile pneumatic clamp designed, developed and manufactured by Quadra. Clamping pressure is variable. Quadra integrated the robot's automation into Kann's existing production line. Its movements are precisely programmed to ensure continuous productivity and reduced cycle times. Recipe parameters can be adjusted from the control station. The visual interface allows the operator to indicate the number
of rows, product position and orientation, as well as the number of products in each row (Fig. 1).
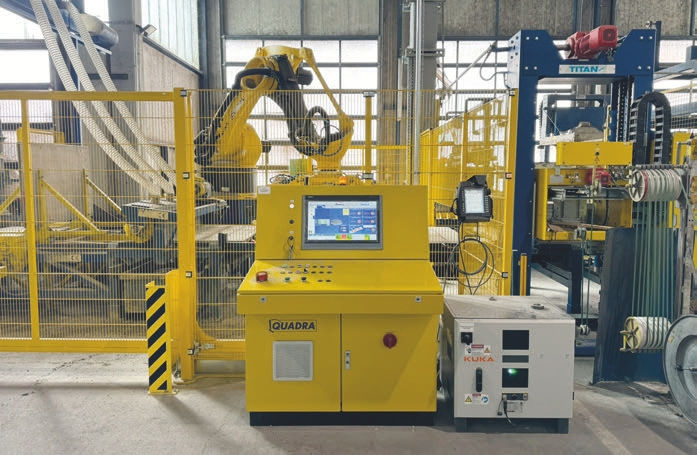
The gripper provides 4-sided clamping, enabling it to grip the products to be placed on the pallet precisely and powerfully. The precision with which the pavers are palletized is remarkable, and the vertical alignment of the products is much more precise than with the conventional method (Fig. 2).


Other advantages of the automated solution are that the linear guidance system for the rails positioned on the handling parts ensures smooth, regular movement, reducing wear and tear and therefore the need for maintenance operations or replacement of the equipment.
What's more, because the trajectories are optimised, movements are reduced compared with conventional palletising methods, generating substantial energy savings.
Personalised service in the customer's language
As part of the operation of its new equipment, Kann benefits from access to the manufacturer's online collaborative platform, specifically developed in German for the occasion. User-friendly, interactive and intuitive, the platform enables Kann to submit requests quickly and easily (information requests, incident reports and quotation requests). They can also access the spare parts catalogue, download technical documentation for their equipment, as well as operating instructions, electrical and pneumatic diagrams, preventive maintenance schedules, safety plans and all certificates of conformity, all in German. On-site training in the use of the equipment was also provided in German.
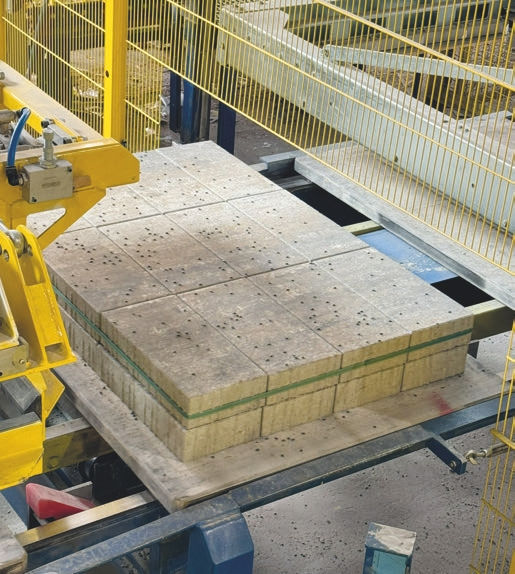

The meticulous preparation of the work on customer site in advance, the effective coordination of the teams involved in the project and the delivery of equipment that had been fully assembled and tested in Quadra workshop contributed to compliance with the specifications and enabled the equipment to be commissioned at Kann in a very short space of time.
Approved by the customer for its performance and ease of use, this first installation by Quadra by Kann is a success both technically and strategically, demonstrating the capacity for innovation and customisation of Quadra and its partners.
Futher Information
KANN GmbH Baustoffwerke
Bendorfer Straße
56170 Bendorf-Mülhofen, Germany
T +49 2622 7070
Quadra
40, route de Findrol
74130 Contamine-sur-Arve, France
T +33 450339221
Comments